Soucieuse d’anticiper les évolutions réglementaires, de maîtriser sa facture énergétique et de réduire son impact environnemental, l’entreprise a engagé dès 2013 une démarche volontaire pour mettre en place un système de management de l’énergie en visant l’obtention de la certification ISO 50001.
Quel a été le déclic pour entamer votre démarche ENERGIE ?
Nous avons constaté que même hors activité notre consommation énergétique atteignait 50% d'un jour de production normal ! Cette prise de conscience a été décisive ! Forts de ce constat, nous avons fait le choix d’aller vers une certification ISO 50001 en 2 temps : d’abord en mettant en place une planification énergétique (ISO 50001 niveau 1) ; ensuite en travaillant pour atteindre la certification complète.
Le diagnostic énergétique a été un choc car il a révélé que la consommation du site un jour férié (le 1er mai), donc hors activité, équivalait à 50% de la consommation d’un jour de pleine activité.
Sur quoi repose votre initiative ?
Nous avons constitué en interne une équipe Énergie dont les membres ont suivi des formations à l’ISO 50001 et aux basiques énergétiques. Cette équipe a participé activement à la définition et à la diffusion des actions, et a joué un rôle central dans la démarche. Elle a été décisive pour impliquer différents services et essaimer efficacement les changements de comportement et d’habitudes. Elle a ainsi travaillé en étroite collaboration avec des groupes de travail ciblés sur les équipements énergétiquement stratégiques.
Les résultats ont été relativement rapides, ce qui a encore renforcé notre motivation et la dynamique ! Aujourd’hui, nous poursuivons notre démarche d’amélioration continue en sensibilisant nos nouveaux collaborateurs et en intégrant systématiquement des recommandations énergétiques dans les cahiers des charges que nous rédigeons lorsque nous renouvellons nos matériels et nos équipements.
Quel a été votre mode opératoire ?
En 2013 nous avons créé une première équipe énergie au sein de l'entreprise pour trouver des solutions de réduction des coûts.
En 2014 nous avons pu réaliser un diagnostic complet du site avec un consultant spécialisé, grâce à l'aide du Conseil Régional et de l'ADEME ; à partir de là nous avons pu installer un comptage et une mesure de nos postes de consommations. Fin 2014 nous avons choisi de nous certifier ISO 50001 niveau 1.
En 2015, grâce à l'action du réseau des CCIs en Limousin, nous avons pu bénéficier d'un parcours d'accompagnement et de formation (123 ENERGIE) qui nous a permis de mettre en place notre management de l'énergie et d'obtenir la certification ISO 50001.
Depuis, nous participons régulièrement avec d'autres entreprises au benchmark proposé dans le cadre du club expert ENERGIE Nouvelle-Aquitaine ; nous y travaillons ensemble sur les problématiques énergétiques pour échanger et mutualiser les bonnes pratiques. Au quotidien nous investissons dans les actions de maîtrise et d'efficacité énergétique pour capitaliser les gains escomptés ; nous sensibilisons les salariés et nouveaux arrivants et nous formons nos référents aux usages énergétiques stratégiques.
Quelles ont été vos actions ?
Nous avons agi sur quatre priorités : Température, éclairage, moteurs, air comprimé, avec de nombreuses actions efficaces.
- Programmation des régulations de température
- Ajustement des puissances d’éclairement + éclairement naturel
- Réduction d’un bar de la pression du réseau d’air comprimé
- Arrêt de l’éclairage pendant les absences
- Arrêt de l’alimentation d’air comprimé pendant l’arrêt des machines
- Arrêt et réduction du chauffage et du rafraîchissement
- Régulation du chauffage avecles conditions climatique
- Réduction de la température d’eau chaude utilisée pour le chauffage des locaux
- Arrêt du raffaichissement des locaux hors période de production
- Arrêt des moteurs de convoyeurs, d’aspiration
Quels résultats mettez-vous en avant ?
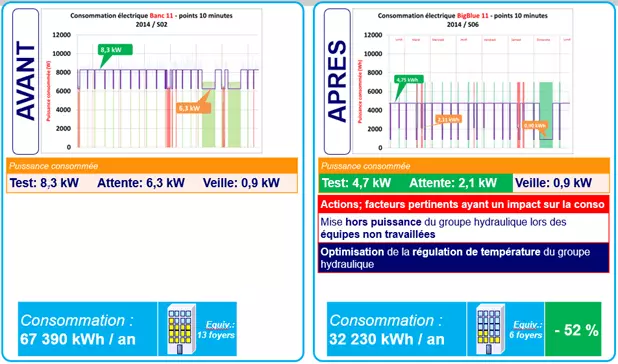
24% d’économies d’énergie sur des machines à laver !
12% d’amélioration de la consommation spécifique pour l’air comprimé
Amélioration de 30% de l’efficacité énergétique pour le chauffage des locaux
Didier Castets Responsable du Service Sécurité Environnement